画像認識を用いた自動検品技術とは?
画像認識を用いた自動検品技術の基本概念
画像認識技術は、コンピュータビジョンの一分野であり、デジタル画像やビデオから有用な情報を抽出する技術です。この技術は、特にディープラーニングを利用することで、大量のデータを学習し、画像内の物体やパターンを高精度で識別する能力を持っています。
ディープラーニングは、多層ニューラルネットワークを使用して、大量のデータから特徴を自動的に学習するアルゴリズムです。従来の機械学習とは異なり、ディープラーニングは画像の前処理や特徴抽出を必要とせず、直接ピクセルデータから学習することができます。これにより、非常に高い精度で画像を解析し、複雑なパターンや物体を認識することが可能になります。
この技術は、医療やセキュリティ、自動運転車など、さまざまな分野で幅広く応用されています。例えば、医療分野では、X線やMRI画像から疾患を高精度で検出するシステムが開発されており、早期診断と治療の精度向上に貢献しています。また、自動運転車では、道路標識や歩行者、他の車両をリアルタイムで認識することで、安全な運転を支援しています。
製造業においては、画像認識を用いた自動検品技術が重要な役割を果たしています。製造ラインでの製品検査を高度に自動化することで、製品の品質を一貫して高いレベルで維持することが可能になります。具体的には、製品が製造ラインを通過する際に、センサーやカメラを使用して詳細な画像を撮影し、その画像をディープラーニングアルゴリズムで解析します。これにより、製品の欠陥や異常をリアルタイムで検出し、迅速かつ正確に不良品を識別して取り除くことができます。
このプロセスにより、製品の品質を一貫して高いレベルで維持することが可能となり、不良品の発生を未然に防ぎ、微細な欠陥を検出して取り除くことで、高品質な製品を提供することができます。
AI技術導入に関する無料相談はこちらから
お問い合わせはこちらAIを用いた画像認識技術の進展
AI(人工知能)を用いた画像認識技術は、近年大きな進歩を遂げています。特にディープラーニング技術の発展により、画像認識の精度と速度が飛躍的に向上しました。
例えば、最新の画像認識アルゴリズムは、製品表面の微細な傷や汚れを高精度で検出できます。これにより、製造ラインでの品質管理が大幅に改善され、企業全体の生産性も向上します。AIを用いた画像認識技術は、製造業において品質管理の精度と効率を大幅に向上させる力を持っています。
さらに、AI技術の進化により、画像認識システムはますます複雑なタスクを実行できるようになっています。例えば、製品の外観検査だけでなく、内部構造の検査や異常な動きを検出することも可能です。
ディープラーニング技術の中で注目されるモデル:
- VGGNet:
- 概要: 非常に深い畳み込みニューラルネットワーク(CNN)であり、シンプルなアーキテクチャが特徴。
- 適用例: 画像分類や物体検出。
- DenseNet(Densely Connected Convolutional Networks):
- 概要: 各層が前のすべての層に接続されているモデル。
- 適用例: 画像分類、物体検出、セグメンテーション。
- MobileNet:
- 概要: モバイルや組み込みデバイス向けに設計された軽量で効率的なモデル。
- 適用例: モバイルデバイス上での画像分類や物体検出。
- EfficientNet:
- 概要: モデルのサイズと計算コストを最適化するためのスケーリング手法を採用したモデル。
- 適用例: 画像分類、物体検出、セグメンテーション。
- YOLO(You Only Look Once):
- 概要: リアルタイムで物体検出を行うためのモデル。
- 適用例: 物体検出、追跡。
- Transformer-based Models(Vision Transformers):
- 概要: 画像処理にトランスフォーマーを適用したモデル。
- 適用例: 画像分類、セグメンテーション。
これらの技術進展により、AIを用いた画像認識技術は今後もさらなる発展が期待され、多くの分野で革新をもたらすでしょう。

画像認識を用いた自動検品技術の独自導入事例
株式会社ケーヒンの導入事例
株式会社ケーヒンは、自動車向け製品の検査工程において、AIを用いた画像認識技術を導入し、目視検査を省人化するプロジェクトを実施しました。このプロジェクトは宮城県の「先進的AI・IoT活用ビジネス創出実証事業業務委託」として実施され、具体的な成果が報告されています。
課題と解決方法
- 検査数の多さ: 1日あたり2000~4000個の製品を検査しており、その中で30~50個の不良が発生。
- 目視検査の限界: 検査員の目の疲労や作業効率のばらつきが課題。
- 人的要因: 体調による作業効率の変化、不良品の見逃しの可能性。
成果
- 過検出の減少: 再学習前の過検出が100個から0個に減少。
- 見逃しの防止: 見逃しも発生せず、判定精度が向上。
- 精度向上: 目視検査とディープラーニング判定の併用により、検査精度が向上。
- データ収集と検証: 5日間の稼働で24万枚の画像を収集し、製品数2.2万個、不良数213個を確認。
この事例から、AIを用いた画像認識技術の導入が製造業の検品工程において非常に有効であることが証明されました。ディープラーニング技術の活用により、目視検査の限界を克服し、検査の効率と精度を大幅に向上させることができました。
フューチャーアーキテクト株式会社の導入事例
フューチャーアーキテクト株式会社は、独自開発のOCRソリューション「Future EdgeAI」を活用し、AI画像検品による入庫業務の自動化を推進しました。新サービス「EdgeAI Batch Inspection」は、パレット単位での一括検品を自動化し、入庫業務の省人化と効率化を実現します。
課題と解決方法
- 手作業の多さ: 検品者が商品の外装バーコードをハンディターミナルでスキャンし、目視で確認する作業が必要。
- 作業負荷の高さ: 賞味期限や製造年月日、数量の確認、書類作成、ラベル貼り付けなど、多くの工数がかかる。
- 効率の低さ: 荷下ろしから倉庫格納までのプロセスが手間と時間を要する。
「Future EdgeAI」を活用し、商品を指定の位置に荷下ろすだけで、スマートフォンが自動で撮影し、AI画像認識により一括検品を行います。これにより、賞味期限や製造年月日、数量などの情報を読み取り、WMS(Warehouse Management System)にデータを連携します。入荷ラベルの自動発行も可能です。
成果
- 作業負荷の軽減: 入庫作業の省人化と効率化により、検品者の作業負荷とドライバーの荷待ち時間を大幅に削減。
- 迅速な検品: パレットごとに一括で検品が行えるため、荷下ろし後すぐに検品が完了。
- 適用範囲の拡大: WMSを利用しない倉庫や、異なる業種での適用も可能。現行業務に合わせたカスタマイズができる。
この事例から、フューチャーアーキテクトの「Future EdgeAI」を活用した画像認識技術の導入が、物流業務の効率化と省人化に大きく貢献することが分かります。多様な業種に対応可能な柔軟性と、高精度な認識技術が、多くの企業での導入を促進しています。
参考リンク
画像認識を用いた自動検品技術の導入メリット
品質管理の最適化
画像認識を用いた自動検品技術は、製造業における品質管理の精度と効率を飛躍的に向上させます。この技術は、高精度な欠陥検出が可能であり、人間の目では見逃しがちな微細な傷や異物も確実に発見します。これにより、製品の品質管理が大幅に改善され、一貫して高い品質を維持することができます。
さらに、自動検品システムは24時間稼働可能であり、常に一貫した品質検査を実施します。これにより、検査員の疲労や判断ミスによるばらつきを排除し、製品の品質を一貫して高いレベルで維持できます。リアルタイムでのフィードバックも可能で、製造プロセス中に即座に対応できるため、欠陥が発見された場合でも迅速に対策を講じることができ、生産ラインの効率を維持することができます。
- 高精度な欠陥検出: 製品の微細な欠陥や異常を高精度で検出。人間の目では見逃しがちな小さな傷や異物も確実に発見し、品質管理の精度が大幅に向上。
- 一貫性のある検査: 自動検品システムは24時間稼働可能であり、常に一貫した品質検査を実施。検査員の疲労や判断ミスによるばらつきを排除し、製品の品質を一貫して高いレベルで維持。
- リアルタイムでのフィードバック: 検査結果はリアルタイムでフィードバックされるため、製造プロセスの中で即座に対応が可能。欠陥が発見された場合でも迅速に対策を講じることができ、生産ラインの効率を維持。
生産効率の向上
画像認識を用いた自動検品技術は、生産ライン全体の効率を向上させる力を持っています。自動検品システムは、高速で大量の製品を短時間で検査することができ、検査工程がボトルネックになることなく生産ラインの全体効率が向上します。
労働力の最適化も図ることができ、検品作業を自動化することで、人間の検査員に代わる自動システムが導入されます。これにより、検査員はより高度なタスクに集中でき、生産性が向上します。リアルタイムでの検品により、製品の欠陥や異常が即座に検出されるため、製造ラインの停止(ダウンタイム)が最小限に抑えられ、ラインの稼働率が向上し、全体の生産効率が向上します。
- 高速検査: 自動検品システムは、高速で大量の製品を短時間で検査。これにより、検査工程がボトルネックとなることなく、生産ラインの全体効率が向上。
- 労働力の最適化: 検品作業を自動化することで、人間の検査員に代わる自動システムが導入され、労働力の最適化が図れる。検査員はより高度なタスクに集中できるようになり、生産性が向上。
- ダウンタイムの削減: リアルタイムでの検品により、製品の欠陥や異常が即座に検出されるため、製造ラインの停止(ダウンタイム)が最小限に抑えられる。これにより、ラインの稼働率が向上し、全体の生産効率が向上。
コスト削減
画像認識を用いた自動検品技術の導入は、コスト削減にも大きな効果をもたらします。高精度な検査により、不良品の発生を未然に防ぎ、再加工や廃棄にかかるコストを削減します。さらに、検査プロセスの自動化により、人件費の削減も期待できます。AIを活用した検品システムは24時間稼働可能であり、労働コストの削減と生産性の向上を同時に実現します。
また、AI技術を導入することで、設備のメンテナンスコストも削減できます。AIは機器の状態をリアルタイムで監視し、予防保全を実行することで、設備の故障を未然に防ぎます。これにより、突発的な機器の停止を防ぎ、安定した生産稼働を維持することができます。さらに、長期的には、AIによる自動検品システムの精度向上と効率化が進むことで、より大きなコスト削減効果が期待できます。
- 不良品の削減: 高精度な検品により、不良品の発生を未然に防ぎ、不良品が市場に出回るリスクを減らし、リコールや返品によるコストを削減。
- 再加工コストの削減: 欠陥が早期に発見されるため、不良品の再加工や修理にかかるコストが削減され、製造コスト全体が低減。
- 人件費の削減: 自動検品システムの導入により、人間の検査員の必要性が減少し、人件費が削減。また、検査員のトレーニングや管理にかかるコストも削減。
これらのメリットを総合すると、画像認識を用いた自動検品技術の導入は、製造業における品質管理、生産効率、コスト管理の全ての面で大きな改善をもたらす重要なステップとなります。導入に伴う初期投資は必要ですが、長期的な運用コストの削減と生産性の向上を考慮すると、その投資効果は非常に高いと言えます。
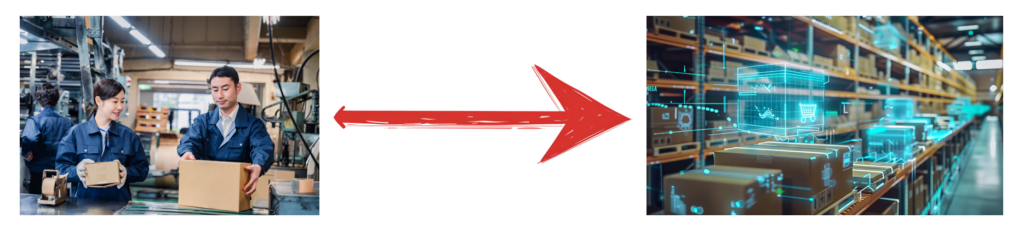
導入プロセスと継続的改善
導入プロセスのステップ
AI技術の導入は、画像認識を用いた自動検品技術だけでなく、他の技術でも、以下のステップを踏むことで効果的に行うことができます。以下に、一般的な導入プロセスのステップを詳しく説明します。
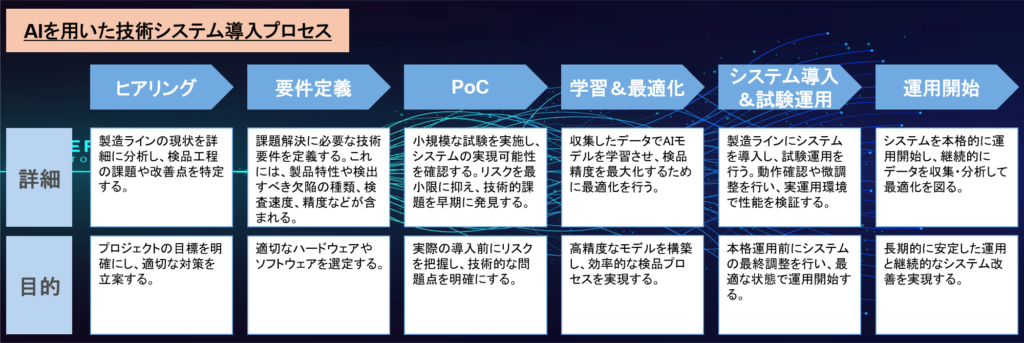
ステップ1: ヒアリング
最初のステップは、企業のニーズを理解し、要件を明確にするためのヒアリングです。この段階では、製造ラインの現状、検品工程における課題、改善したい点、期待する成果などを詳細にヒアリングします。これにより、プロジェクトの目標や方向性を明確にし、関係者全員の理解を一致させます。例えば、現状の検品方法がどのように行われているか、どのような欠陥が発生しているのか、そしてそれらをどのように検出しているかを詳細に理解します。加えて、企業が目指すべき検品精度やコスト削減目標を明確にし、システム導入の基準を設定します。このヒアリングプロセスは、プロジェクトの成功に不可欠なステップです。
ステップ2: 要件定義
ヒアリングで得た情報を基に、具体的な技術要件を定義します。ここでは、検品対象の製品特性や検出すべき欠陥の種類、検査速度、精度などを詳細に記述します。また、製造環境に適したハードウェアやソフトウェアの選定も行います。例えば、製品の大きさや形状、表面の状態などを考慮し、適切なカメラやセンサーを選定します。さらに、システムが処理できるデータ量や応答時間も考慮し、最適なハードウェア構成を設計します。この段階で明確に定義された要件は、システム設計と開発の基礎となり、後のステップでのスムーズな進行を保証します。
ステップ3: PoC (概念実証)
PoC(Proof of Concept)は、提案された技術やシステムの実現可能性を検証するプロセスです。この段階では、実際の製造ラインに導入する前に、小規模な試験を行い、システムの有効性やパフォーマンスを確認します。PoCは、プロジェクトのリスクを最小限に抑え、技術的な課題を早期に発見するために重要です。例えば、小規模な製造ラインでテストを行い、システムが期待通りに動作するかを確認します。このテストにより、システムの欠陥や改善点を特定し、必要な修正を行います。PoCの成功は、プロジェクトの本格的な進行を後押しし、投資の正当性を証明するために欠かせません。
PoCの重要性: PoCは、AIシステム開発において最も重要なフェーズです。これは、技術の実現可能性を確認し、全体のプロジェクトの方向性を確定するためです。ここで得られる結果が、最終的なシステムの設計や導入に大きな影響を与えます。したがって、このステップでの成功は、プロジェクトの成功に直結します。また、PoCに失敗した場合、早期に問題を発見して対応策を講じることで、後の段階での大規模な修正を防ぐことができます。
ステップ4: 学習&最適化
PoCの結果を基に、AIモデルの設計と訓練を行います。このステップでは、収集したデータを使ってモデルを学習させ、検品精度を最大化するための最適化を行います。モデルの最適化は、システムの性能を向上させるために重要です。(例えば、過去の検品データを用いてモデルを訓練し、検品精度を高めます。)さらに、アルゴリズムを調整し、検品速度を向上させることで、製造ライン全体の効率を向上させます。また、定期的なモデルの再訓練を行い、新たなデータや条件に対応できるようにします。最適化されたAIモデルは、製品の品質を確保するための重要な要素です。
ステップ5: システム導入&試験運用
設計と学習が完了したら、システムを製造ラインに導入し、試験運用を行います。この段階では、システムの動作確認や微調整を行い、実際の運用環境での性能を検証します。試験運用により、システムの実用性と信頼性を確認します。例えば、実際の製品を使って検査を行い、システムの精度や速度を評価します。必要に応じて、パラメータの調整やシステムの改良を行い、最適な動作状態を実現します。試験運用の結果を基に、システムの最終調整を行い、本格運用に備えます。これにより、導入されたシステムが期待通りに機能することを確認します。
ステップ6: 運用開始
試験運用の結果を基に、システムを本格的に運用開始します。運用開始後も継続的にデータを収集・分析し、システムの最適化を図ります。これにより、システムの効果を最大限に引き出し、長期的な運用の安定性を確保します。必要に応じて、モデルの再訓練やハードウェアのアップグレードを行い、システムの性能を維持します。継続的な改善プロセスにより、システムは常に最新の状態を保ち、高い品質管理を実現します。
参考リンク
Fiby株式会社のサービスとサポート
導入支援とカスタマイズサービス
Fiby株式会社では、お客様のニーズに合わせたAI導入支援とカスタマイズサービスを提供しています。初期のヒアリングから要件定義、システム設計、導入、運用まで、全てのプロセスをサポートします。これにより、効率的かつ効果的な検品システムや業務効率化ソリューションを実現します。
また、AI導入やビジネス・開発推進に関する無料相談を提供しています。無料相談では、過去の他社事例を共有しながら相談された課題に対してどういうアプローチがあるか検討し、プロジェクトの具体的な実現可能性について確認します。お客様の具体的な課題やニーズに応じたソリューションのご提案をいたします。私たちとともに、AI技術を活用してビジネスの効率化と成長を実現しましょう。